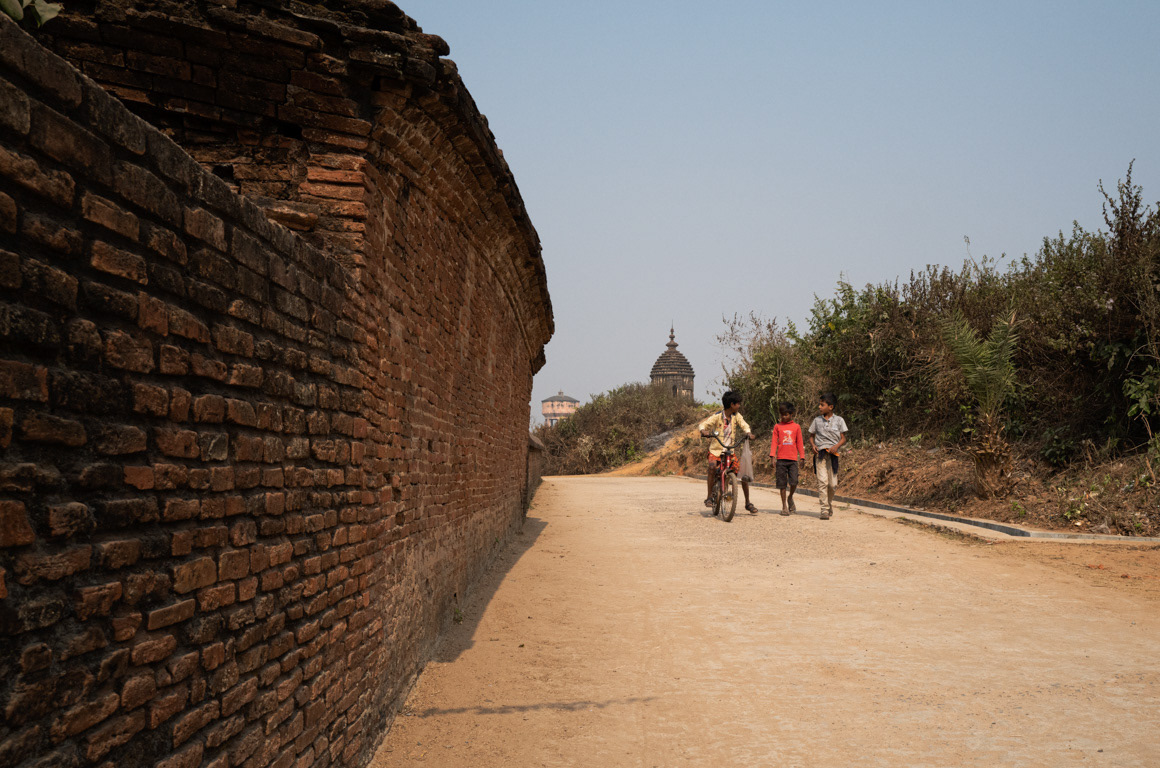
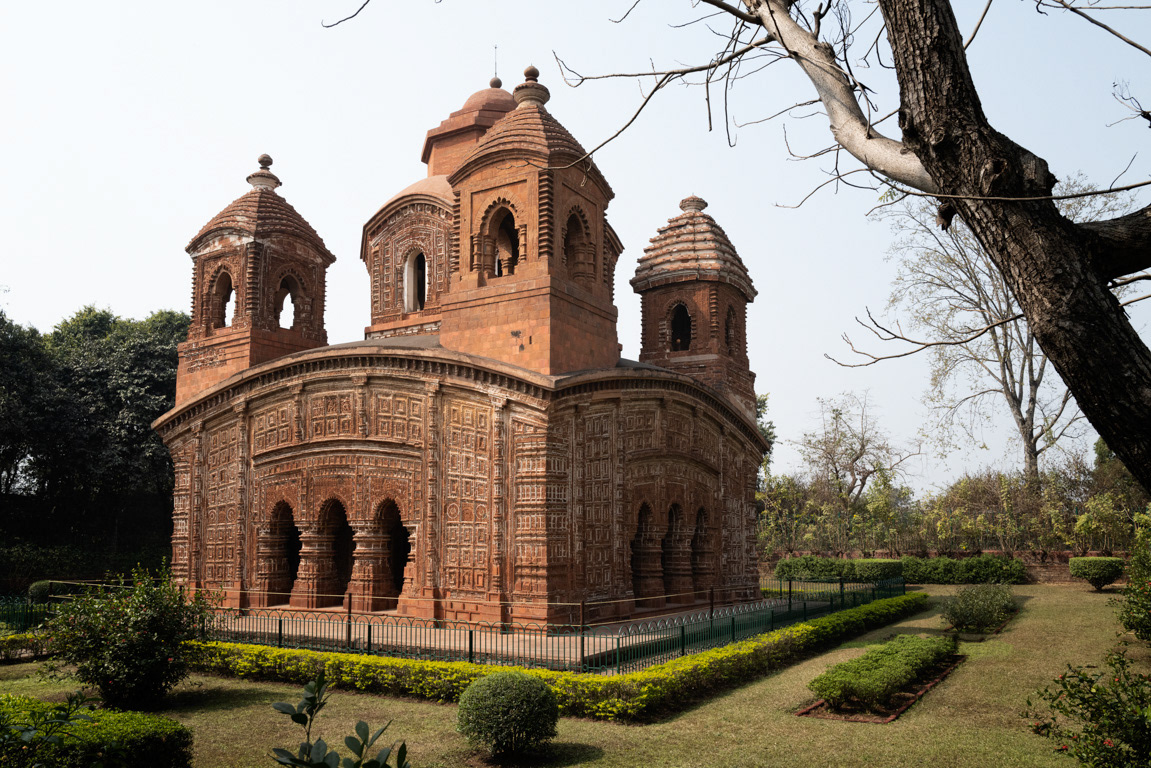
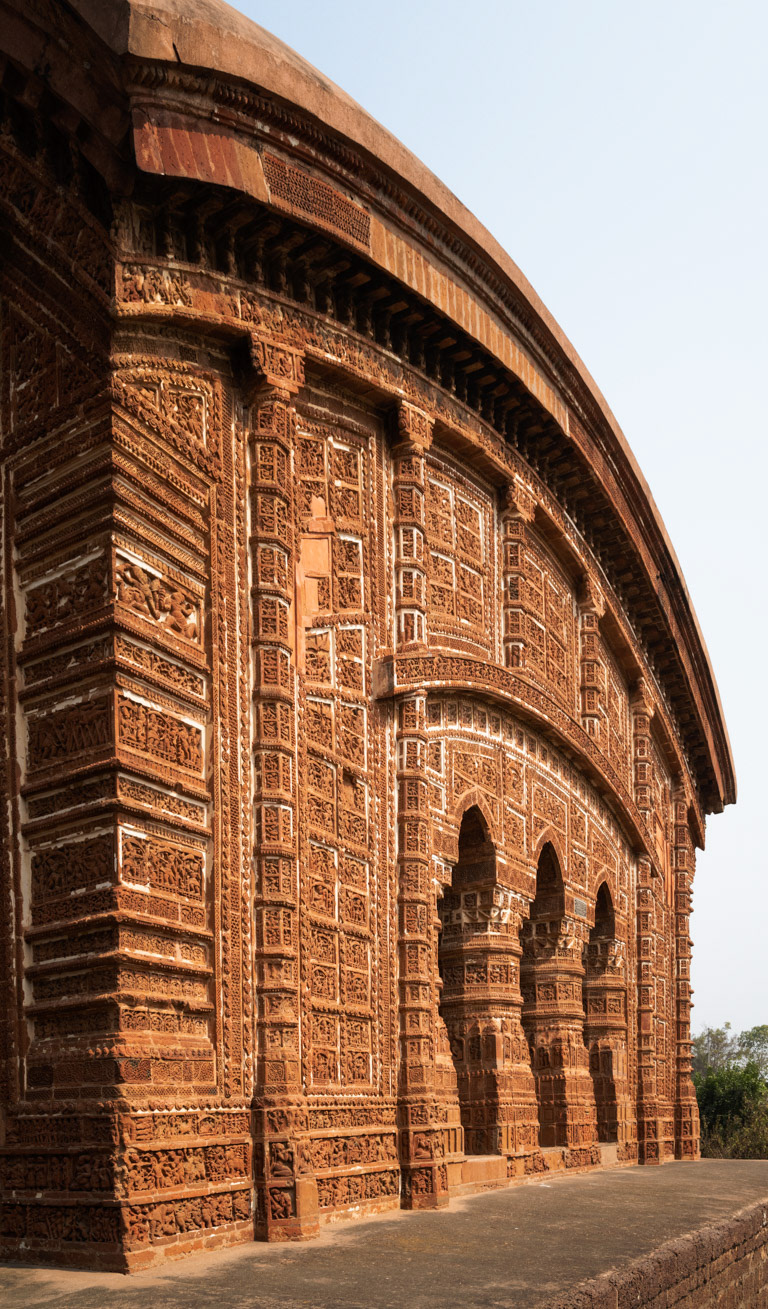
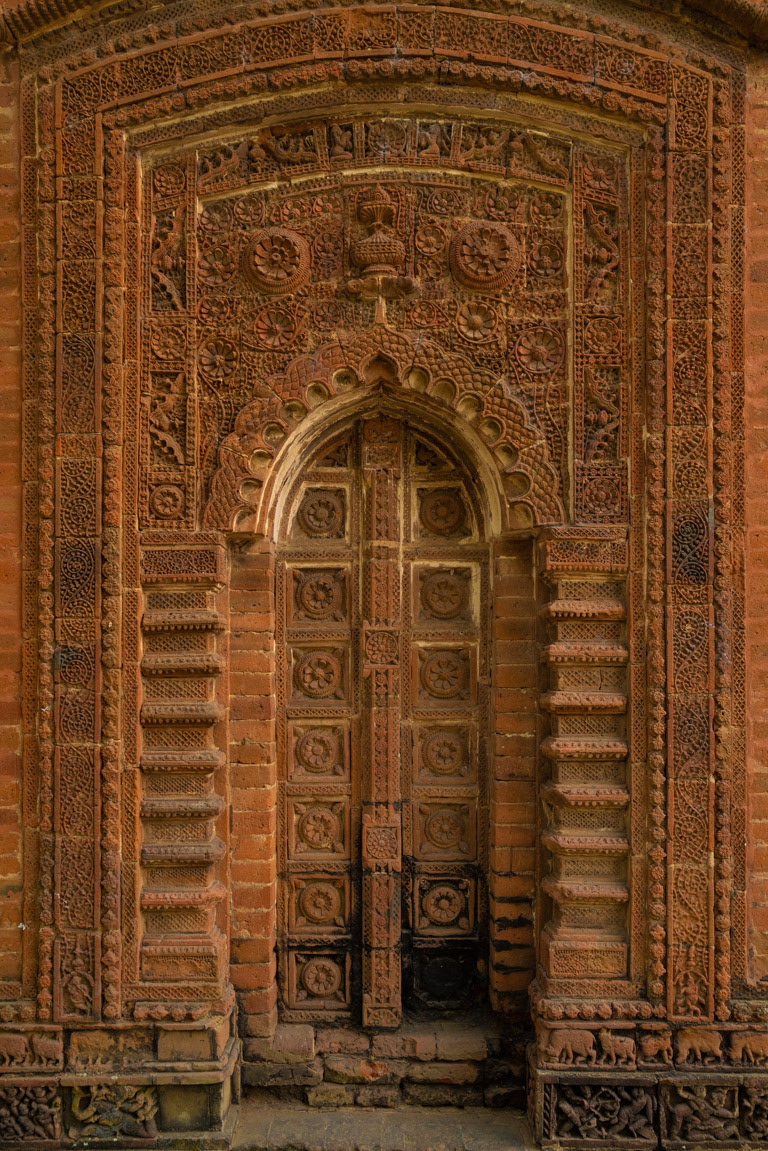
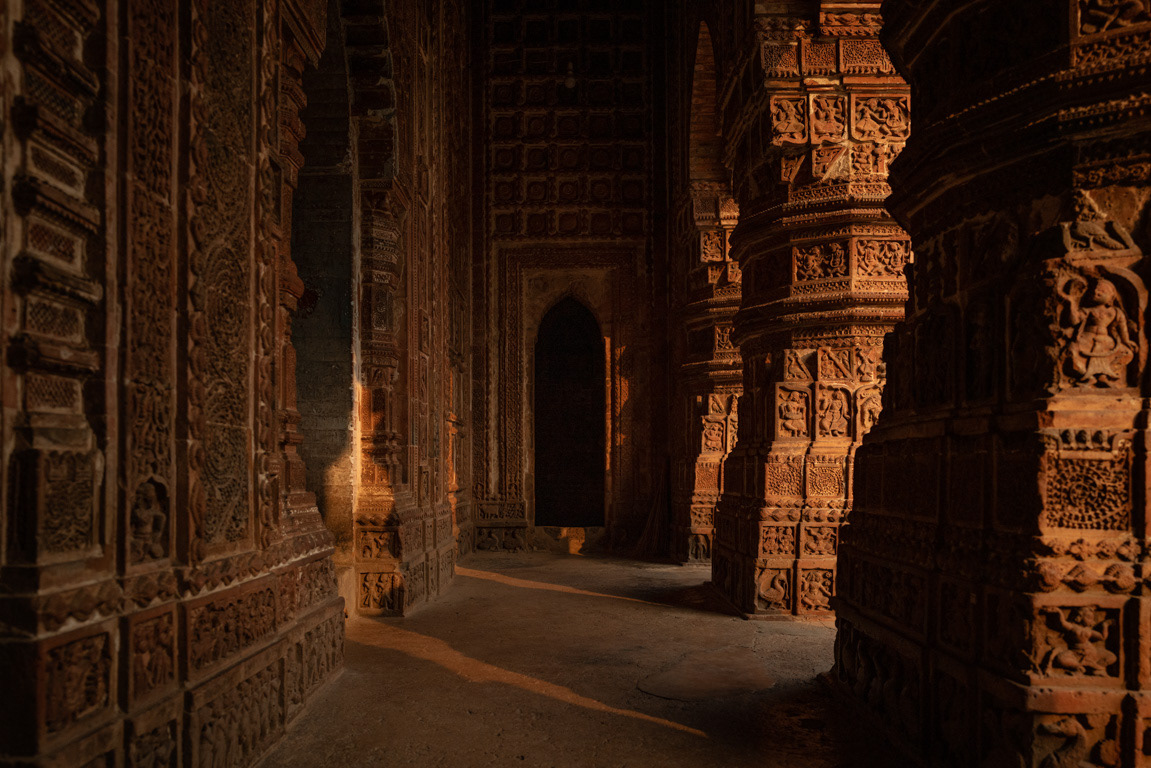
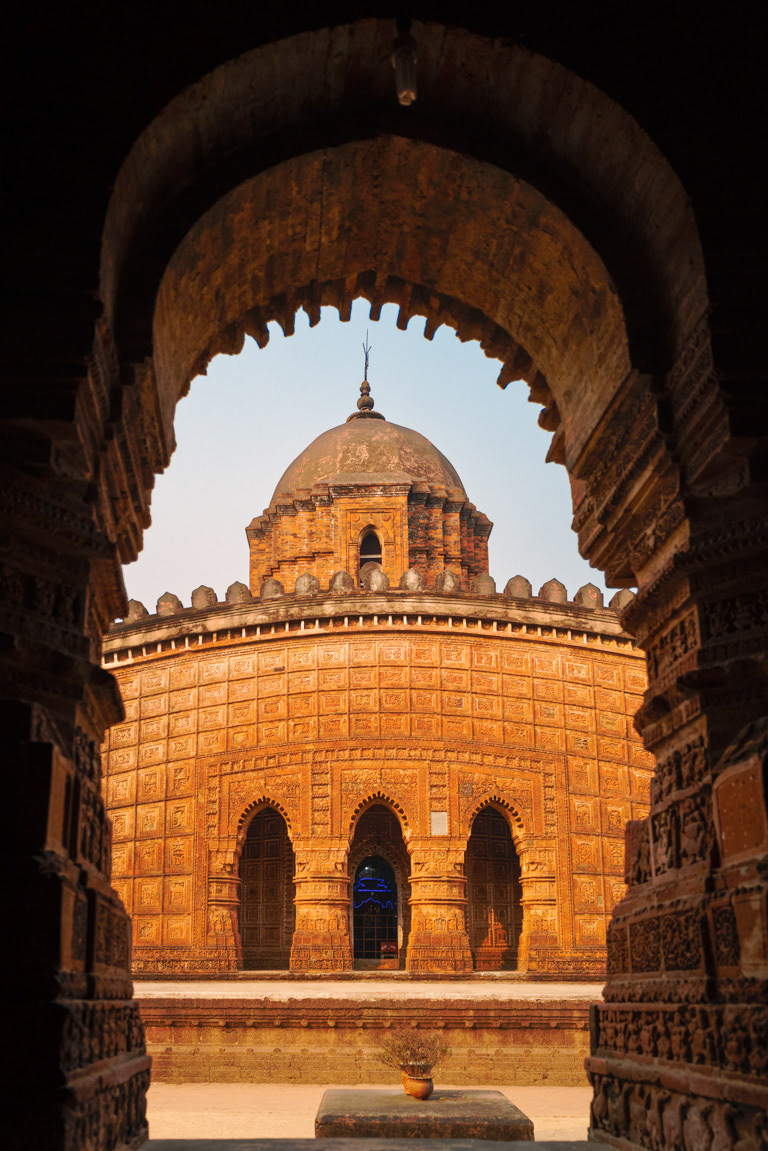
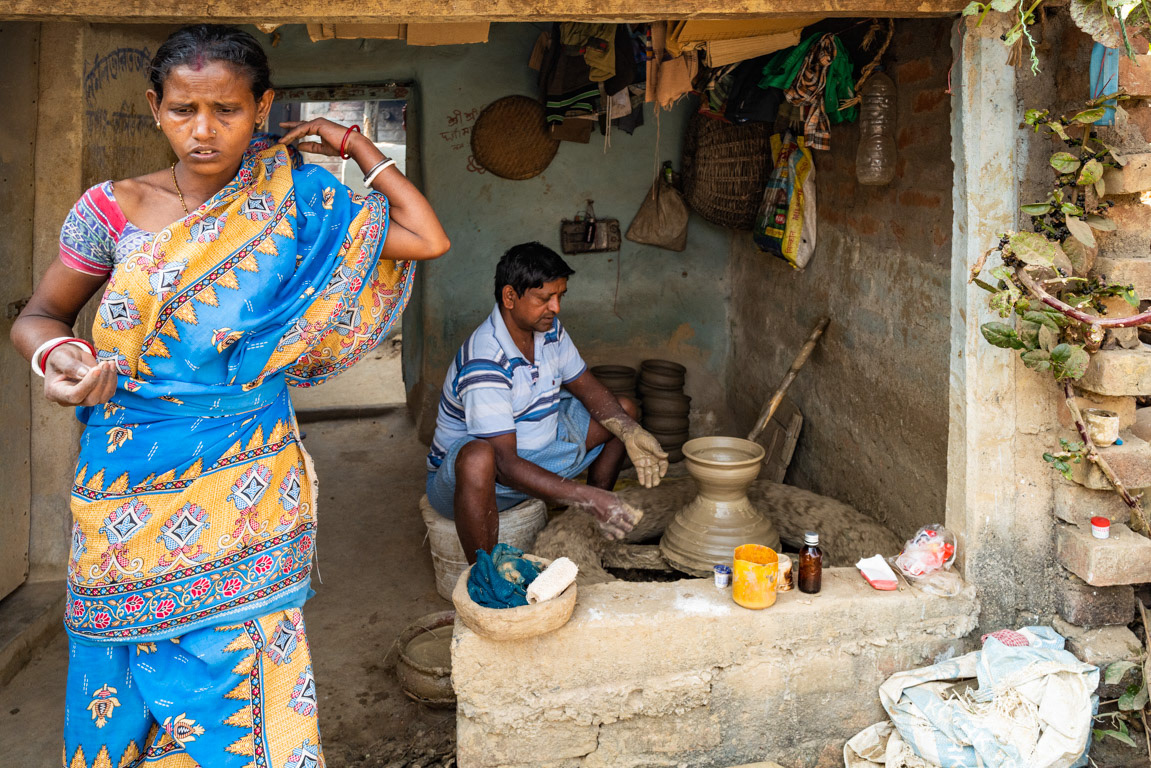
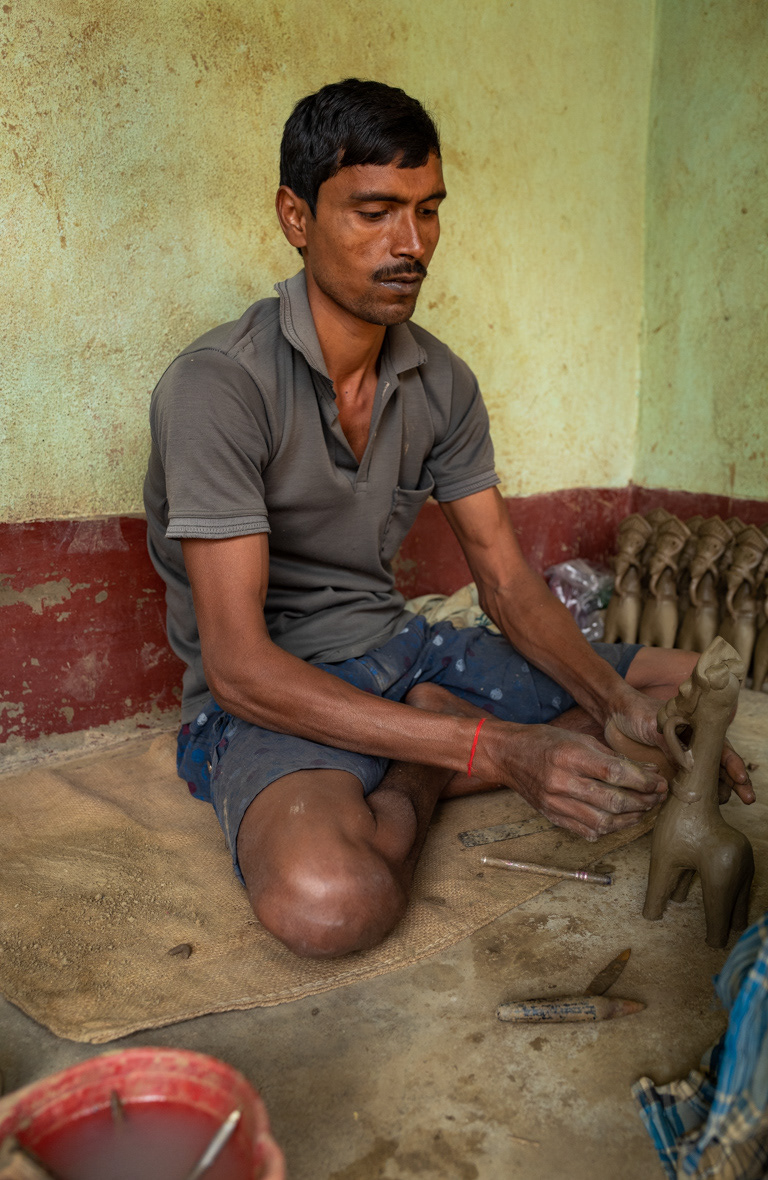
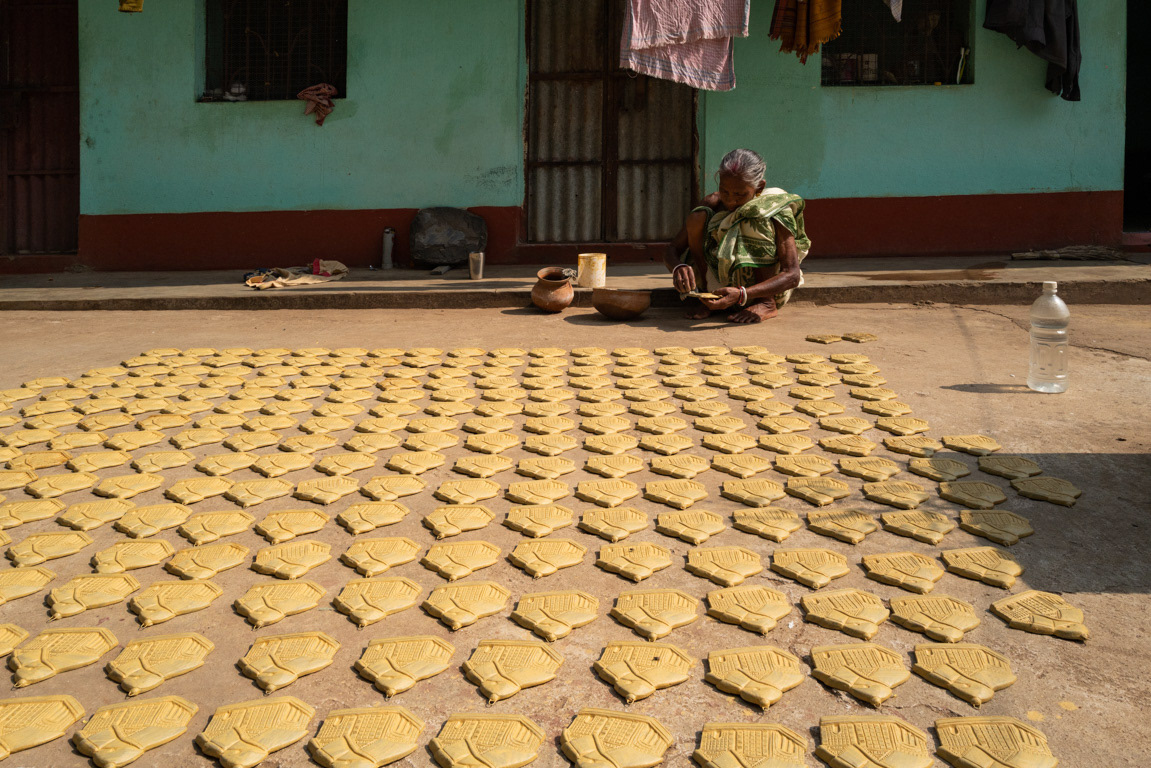
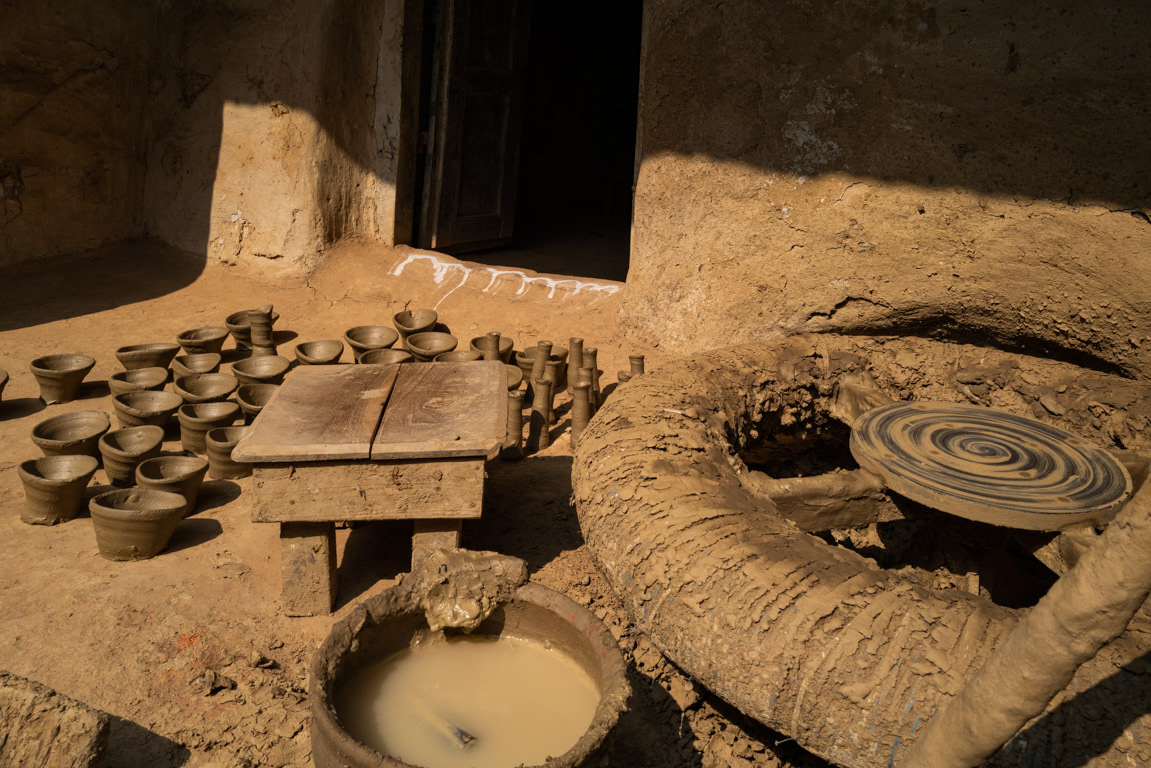
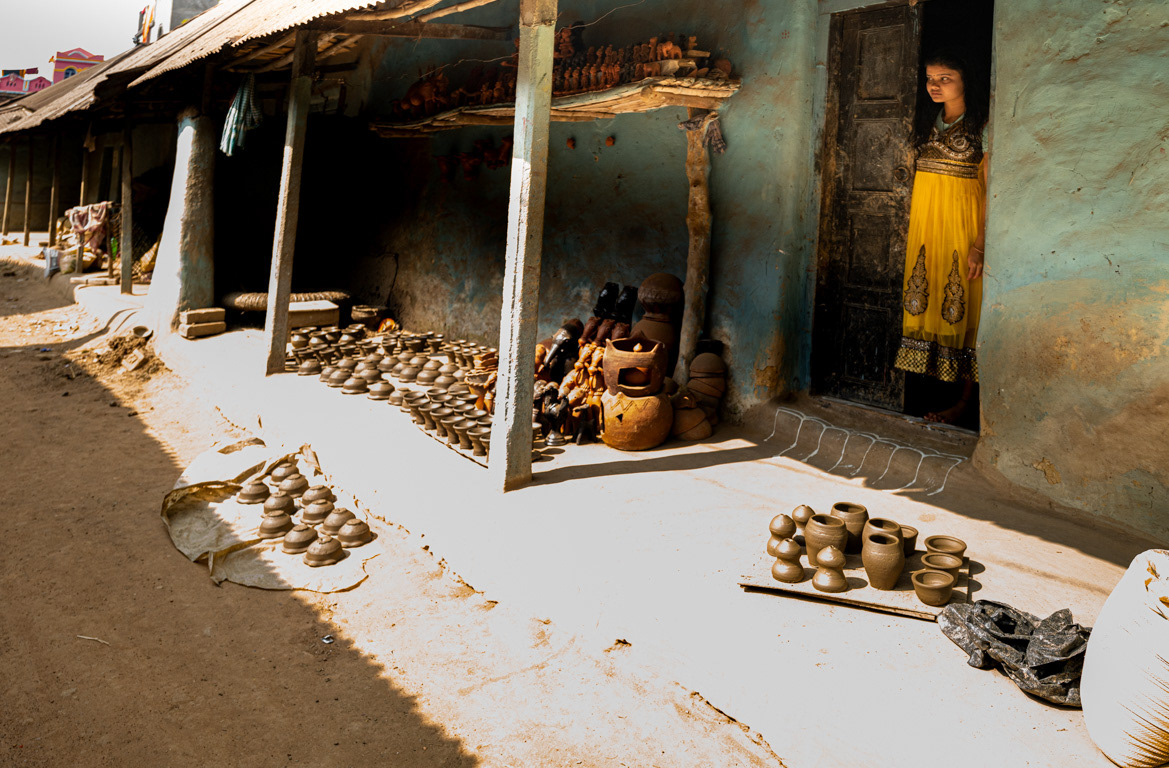
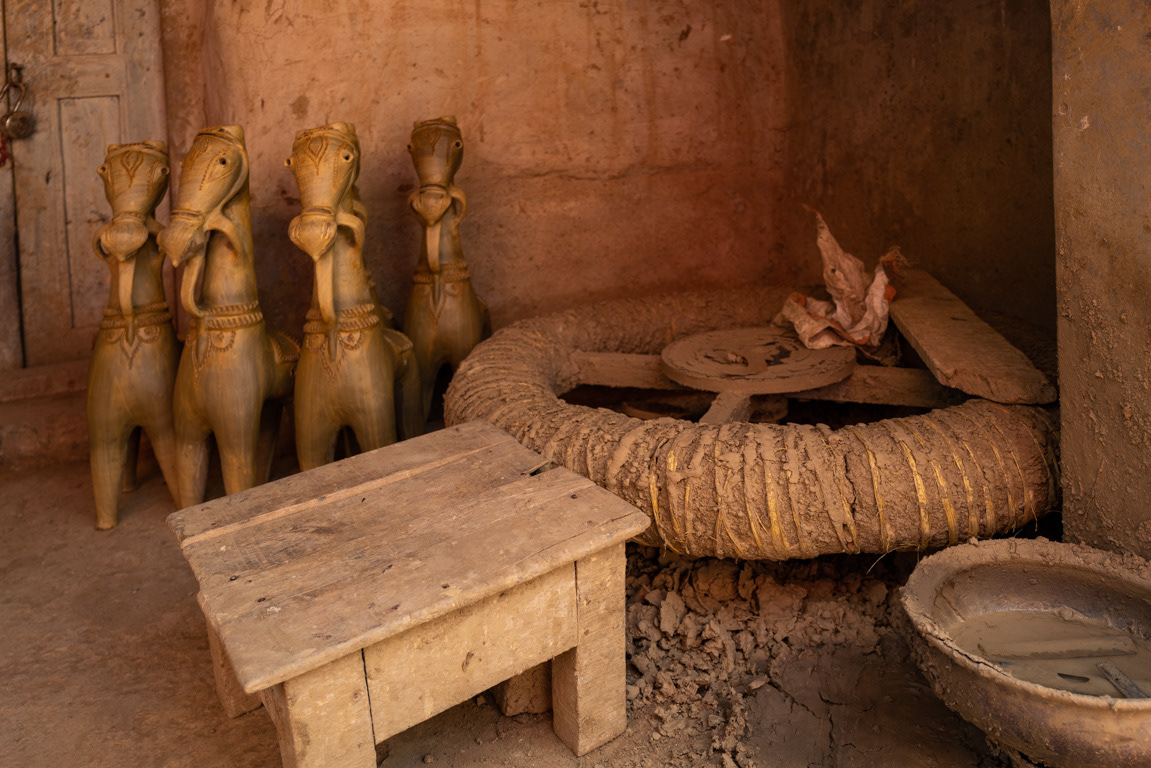
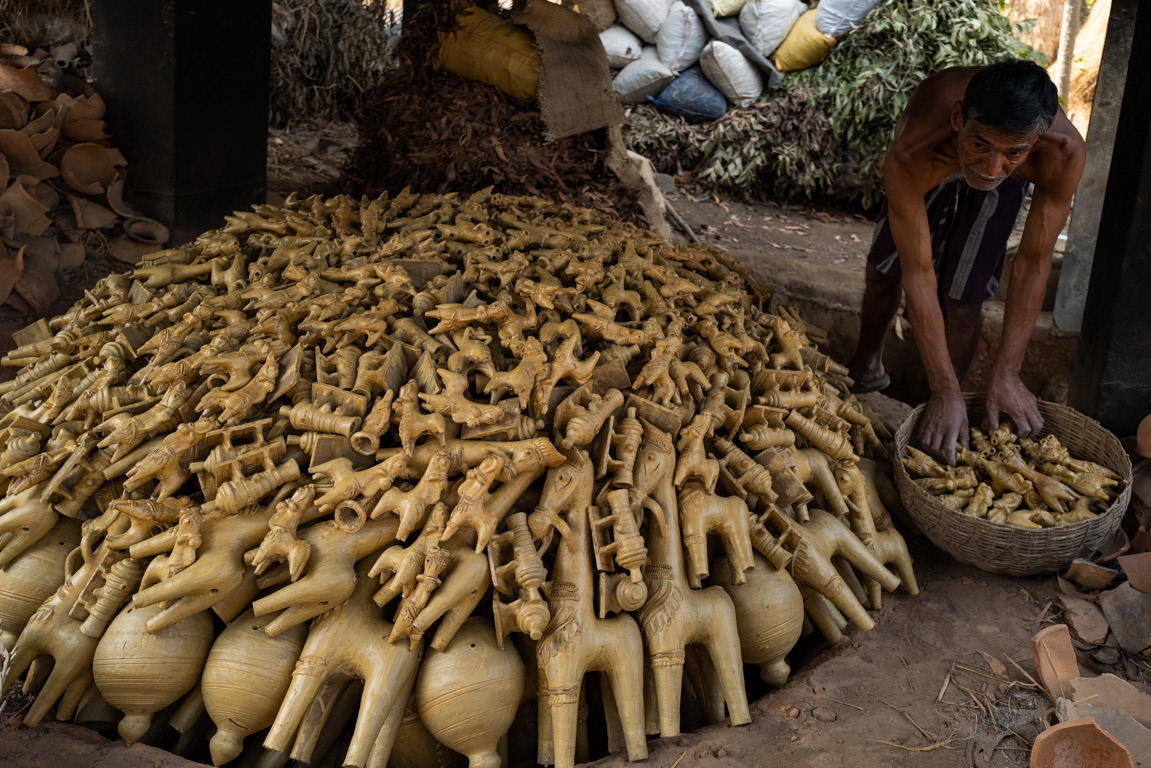
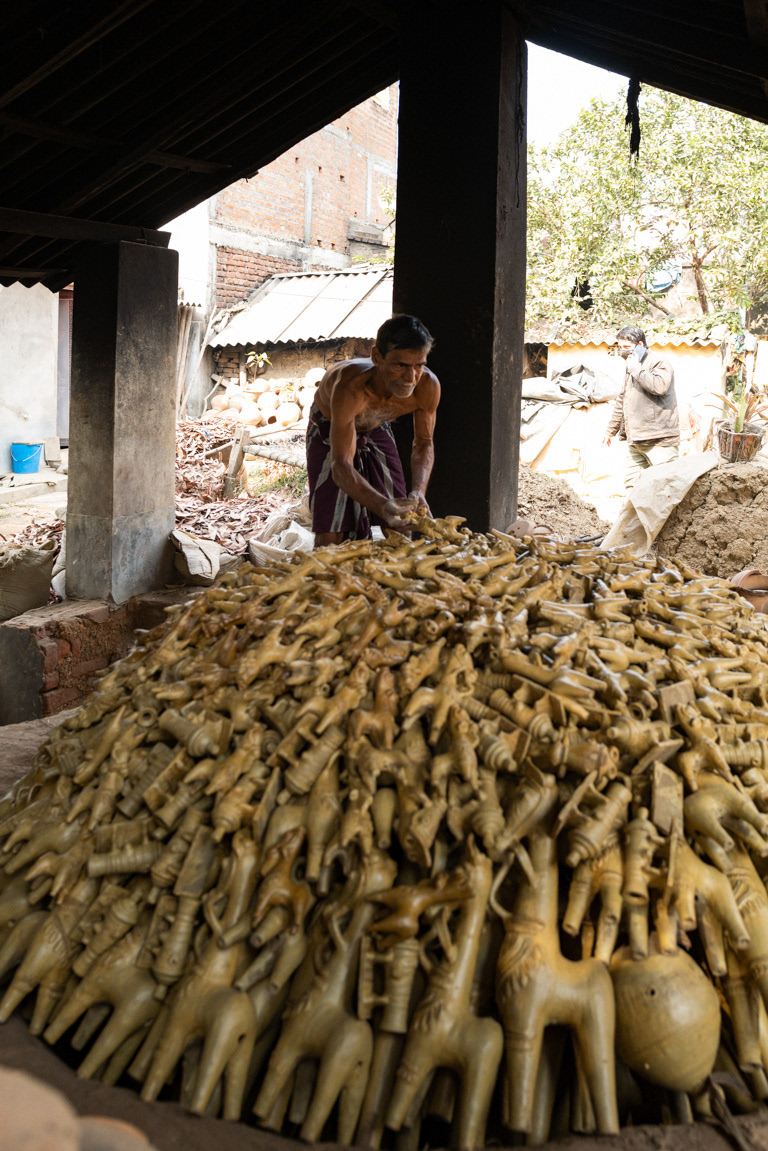
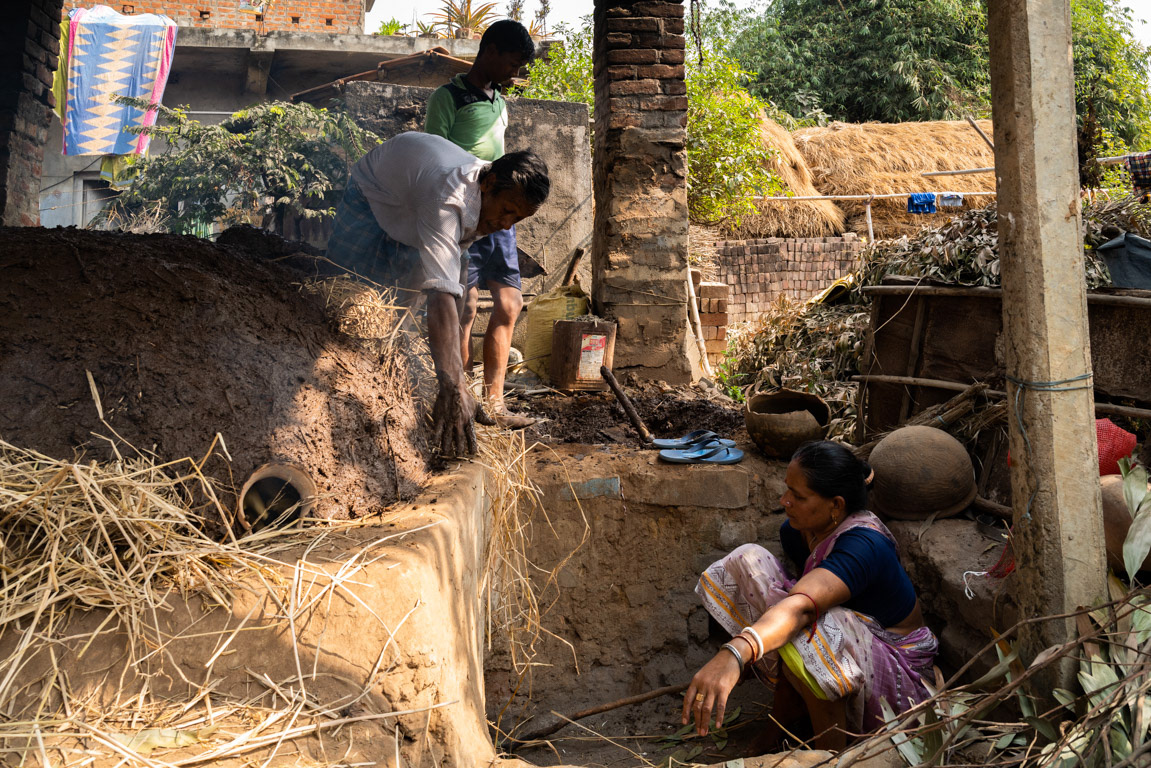

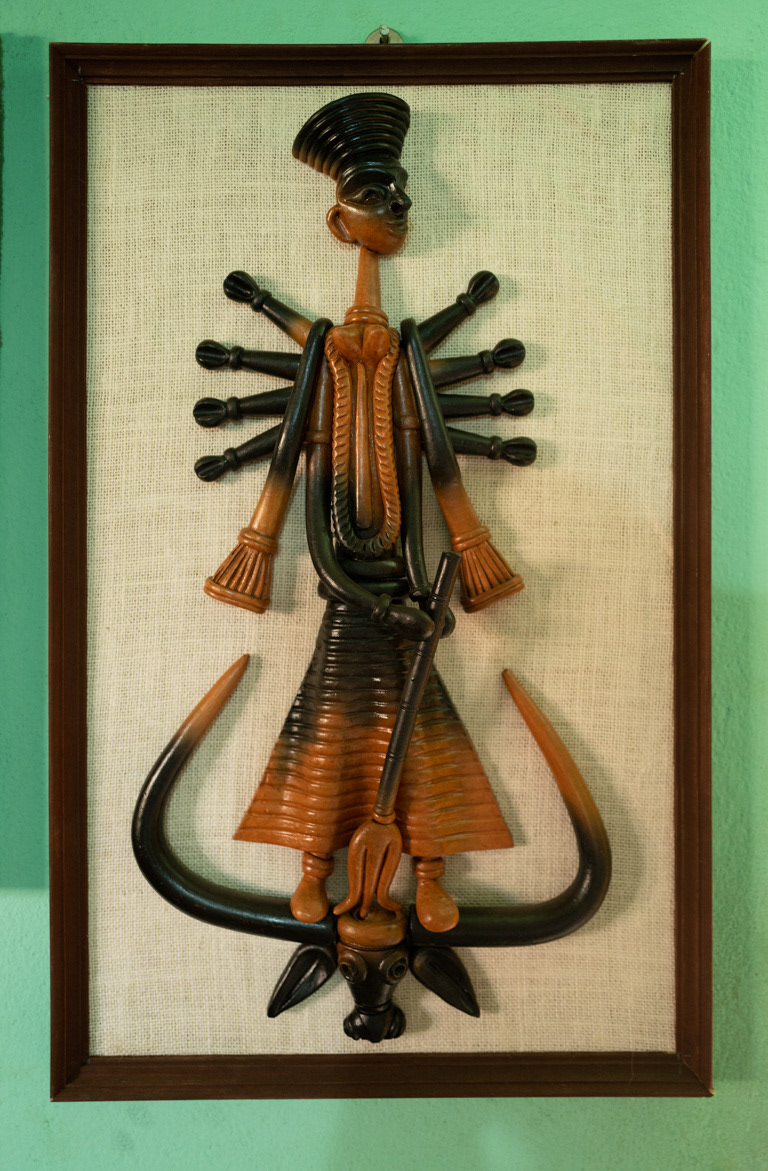
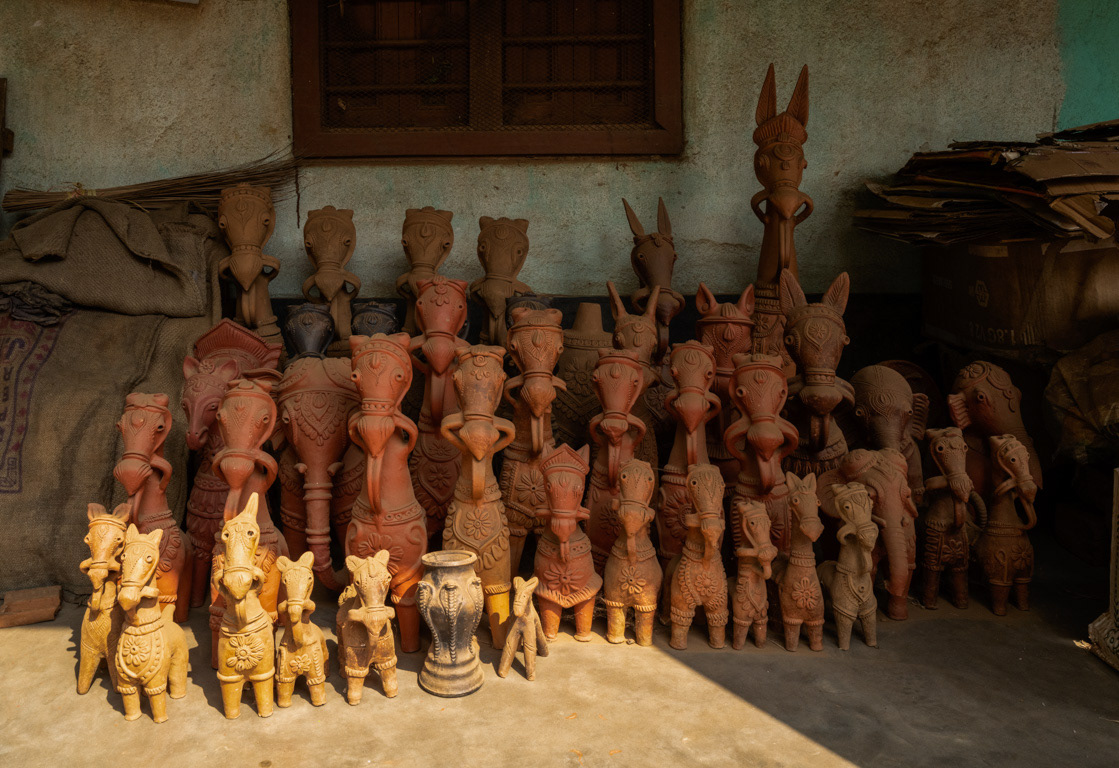
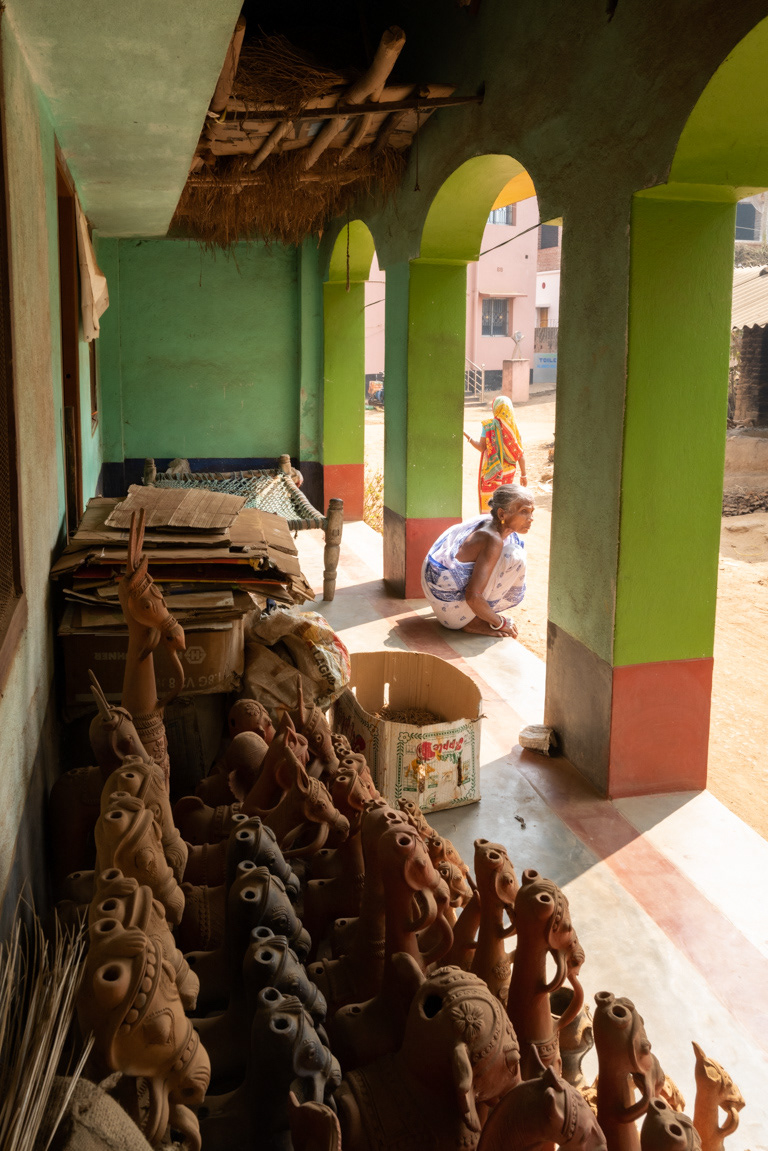
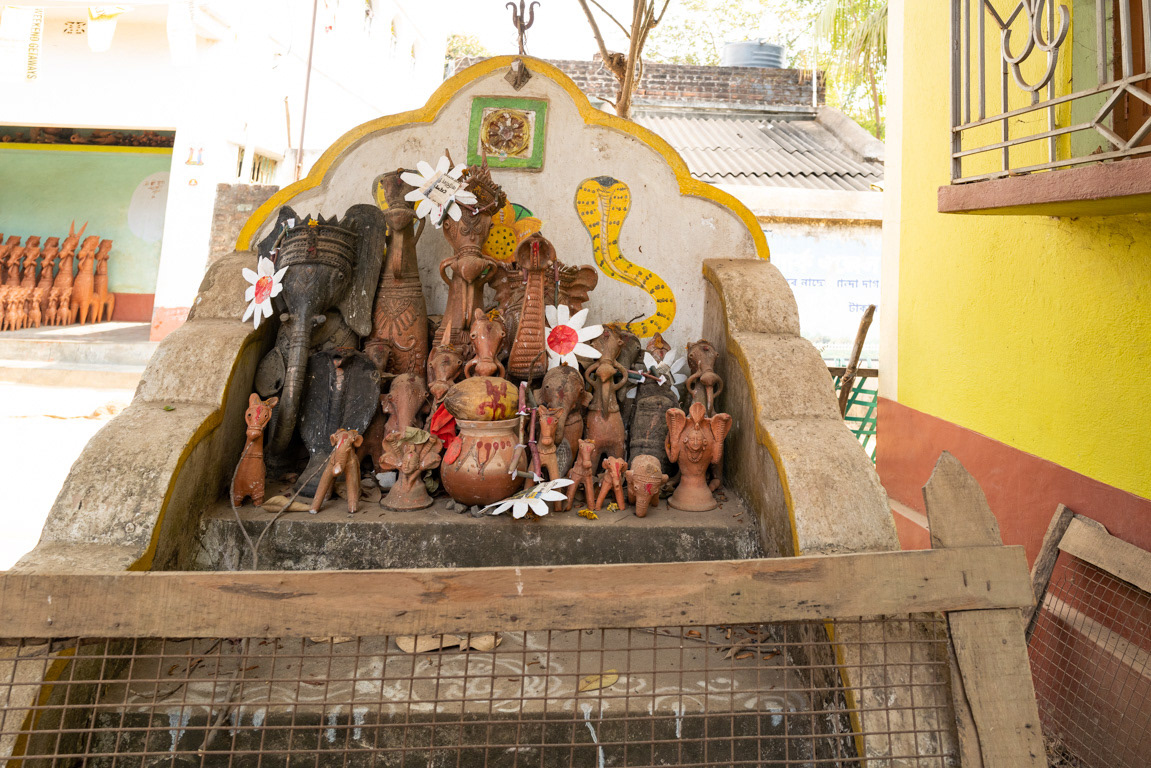
VILLAGE OF TERRACOTTA The temples and shrines in Bishnupur are known for their remarkable architecture and craftsmanship. The Shyam Rai temple, made of baked bricks was built by King Raghunatha Singh, in 1643 to honour Lord Vishnu. The style of the temple is an amalgamation of Panchranta and Gandhar that is reflected in the pillars and arched gateways. The bricks contain intricate engravings and the temple is adorned with terracotta sculptures depicting stories of Krishna from the great Indian epics like Ramayana and Mahabharata. The walls, portico, and pillars contain scenes from the epics, crucial to the culture of the place. These terracotta products are sourced from a village located at a distance of 22 km away from Bishnupur called Panchmura. Terracotta is essentially burnt or baked soil. At present, the village consists of almost 88 families, of which men and women are involved in the entire process of crafting and chiselling the clay with their hands with utmost perfection, making it a 1000-year heritage. The art is linked closely to the community of kumbhakars, as they take time to fine-tune their skills. Terracotta initially was invented and popularized for the religious rituals of the village. Terracotta tribal art of Panchmura showcases its roots with the strong and sharp geometric lines and curves sculpted along with the facial features of the statues. The raw materials, tools, and finishing touches are all obtained and completed in the village; hence, it embodies the essence of authenticity. A lump of clay is formed from the alluvial soil found in the village, with a little amount of sand and freshwater fetched from the pond specifically. The clay is then pressed and put on a wheel and moulded to create many pieces such as idols of gods and goddesses, horses, elephants, and other artefacts. It is baked in the sun in mud kilns with dry eucalyptus leaves. The Bankura horse made from terracotta is famous all over the world and is the logo of All India Handicrafts. The different parts of the body of the horse are made separately and then put together. The uneven bits are smoothened and let to dehydrate in a closed room at normal temperature for about 6-7 days. Then, they are heated in the sun and burnt. Two kinds of colours can be achieved naturally for the horses, a regular reddish-brown shade and black by carefully sealing the vents and playing with the smoke as required. The structure of the horse is passionately fashioned by the artisans as a testament to devotion and valour. This craft goes beyond merely being a livelihood for the families, it has folklore woven into every piece that is created.